The Research And Development Process At Cold Air Inductions
When it comes to performance cold air intakes, you don’t want the same old heat-absorbing plastic system. You want a durable, solid (yet lightweight) system with an overall design that will keep the intake air cool as possible. That’s where CAI cold air intakes excel.
CA intake systems feature high-performance air filters, thermal-coated tubes, and insulated air boxes. All these parts are designed to specs above and beyond the industry standard. Our intake development process starts with CAD engineering. We use the same development tools employed by automotive manufacturers, but we don’t stop there. Read on to learn all about our R&D process, and why the end result is a step above the rest.
The Start: Design
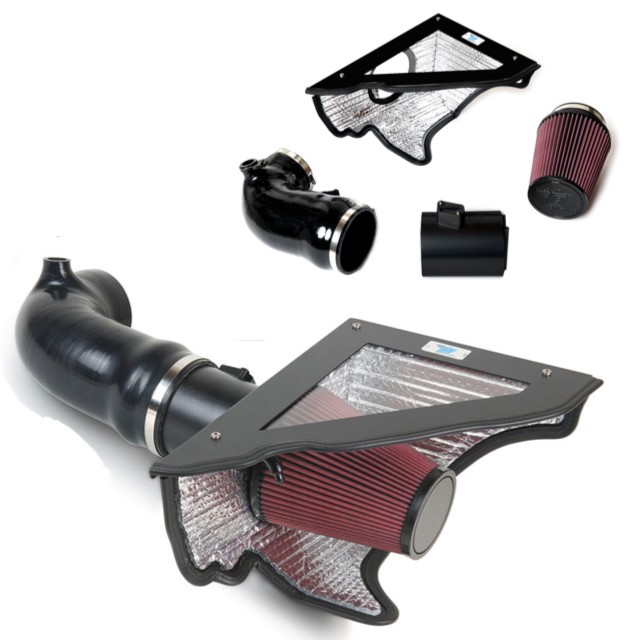
Our process starts with a review of the original equipment manufacturer’s (OEM) air intake. We test it to identify flow restrictions and gauge how they impact mass airflow sensor readings. We examine the size and spacing of the OEM components and measure the airflow and air intake temperatures. Using what we learn, we develop a mathematical engine performance and efficiency model to guide product development. This becomes our blueprint for product development.
Up Next: Development
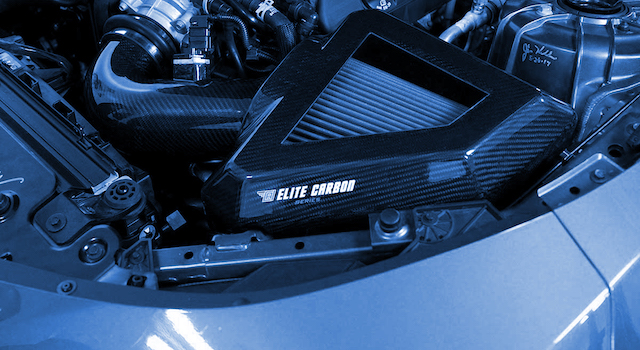
The next step is to prototype several potential designs and complete preliminary testing. The goal of this phase is to identify the best prototype. Once the best prototype is found, we then refine the design based on performance testing results.
While our exact testing systems and procedures are proprietary, we can share the three main types of tests we run:
- Air Flow Restriction Testing: We measure airflow in several standard conditions (e.g., idle, 1/2 throttle, WOT, etc.)
- Thermal Testing: We measure the temperature of the air flowing into the engine
- Engine Performance Testing: We measure fuel flow and engine torque
Once a winning prototype is developed through the testing methods above, it’s time to start engineering.
As you can imagine, the test results depend upon one another. When airflow restriction decreases, or temperatures drop, engine performance will improve. Understanding the interdependence of these tests is one of the keys to our success. They provide the tools and data to model airflow and engine performance in a way that few other companies can match.
In fact, Cold Air Inductions is one of the only companies selling aftermarket air intakes and is also a Tier 1 OEM supplier. When automakers need a performance air intake designed, they call CAI.
Building It: Engineering And Manufacturing
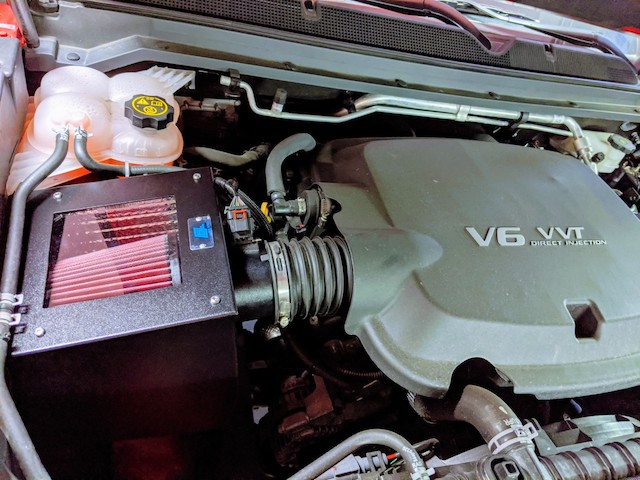
The winning prototype then transitions into a mass-produced product. This stage involves turning the prototype into a digital model and developing tooling needs. The first few units off the line have to be rigorously tested. We’re not just ensuring the product performs like the prototype – we’re also focused on durability, fitment, and quality.
The Final Step: Production
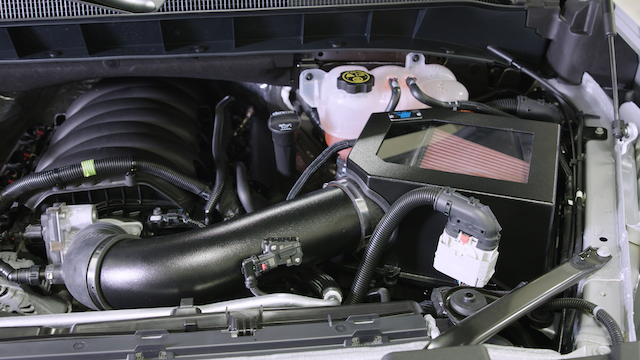
Once the production samples meet our quality and performance standards, full-scale production begins. We start marketing the product on social media and alert our dealers about the upcoming product release. We also fine-tune the installation instructions and produce installation videos.
Throughout the entire process, we emphasize:
- Reducing airflow restrictions to maximize performance
- Minimizing heat soak. The air going into the engine should be as cool as possible for maximum density and performance
- OEM grade fit, finish, and function. All CAI products are durable, easy to install, and trouble-free
Remember, Cold Air Inductions is a Tier 1 OEM supplier. As such, we have to follow a very rigorous design, development, and production process. The result? Guaranteed optimal fit, finish, and performance.